Region: Asia
Territory: Taiwan
Category: Energy Saving
Image left: AVF Pump Installed
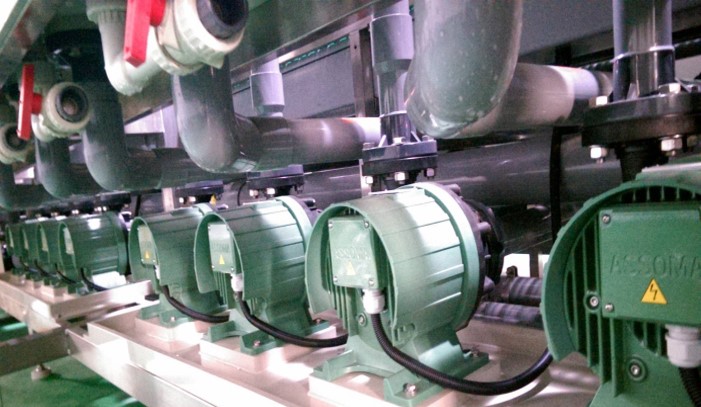
Situation
The customer uses a Vertical Continuous Plating system to produce several different printed circuit products. Each product has its own production needs and the customer runs the pumps at 30, 44, and 50 Hz to cater to the different flow capacity and pressure needs.
Challenge
The pumps are equipped with induction motors controlled by inverters. At the lower pump speeds, the motor efficiency drops significantly. Since existing pumps are our AMX-series models, the customer consulted with us to get our thoughts on options to meet their energy goals.
Figure 2. AVF Pump
System Layout
One section of the plating line consists of six pumps working in parallel. Each pump feeds into a filter followed by spray nozzles in the plating tank. Process is monitored using a flow meter installed after the filter. To ensure process stability, all six pumps must provide the same operating pressure.
Solution
Replace one of the pumps with our AVF model and install a set of power monitors to record energy consumption. Since the pump speeds change with the product, the total power consumed by both pumps is recorded after 29 days in operation (shown below)
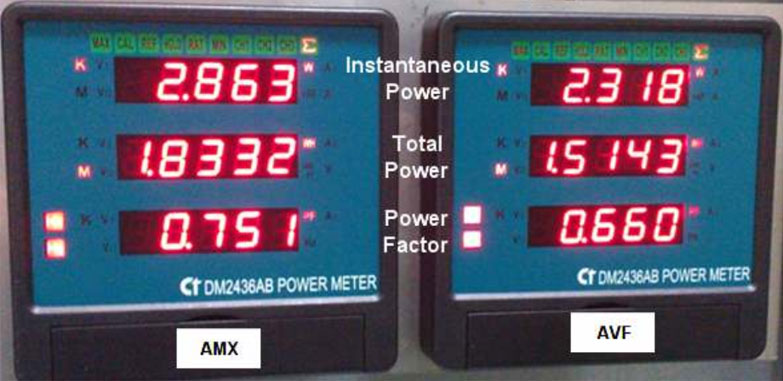
Figure 3. Power Savings after 29 days
Results
Over a period of 29 days, the power consumption difference between the pumps is 318.9 kWh. An additional observation was taken on the 104th day with total energy saving of 1,228.9 kWh. The customer realized an average energy cost savings of 20% by switching from our AMX series pump to the AVF series pump.
Financial Analysis
- 20% savings on energy costs
- Reduced maintenance costs
- Reduced production down-time