What is the duty point of an application?
The duty point of the application is the point on the pump curve at which the pump operates. It is a combination of flow rate and head for the application. The flow rate is how fast the liquid is being moved by the pump through the system. Common units are liters per minute, cubic meters per hour, cubic feet per second, and gallons per minute. The total head of the system includes two parts: the amount of height we are lifting the liquid (static head), and the head loss as the liquid moves through the system (frictional loss). We will look in more detail at the concepts of flow rate and head in the following sections.
Common Ways of Determining the required Flow Rate
If you search for ways to determine flow rates, you will find articles describing scientific methods of measuring flow rates in an existing system. That is great, but what can we do when we are in the process of designing the system? It turns out there are several ways to arrive at the desired flow rate for our system. We shall look at three practical methods.
Method 1: Transfer rate
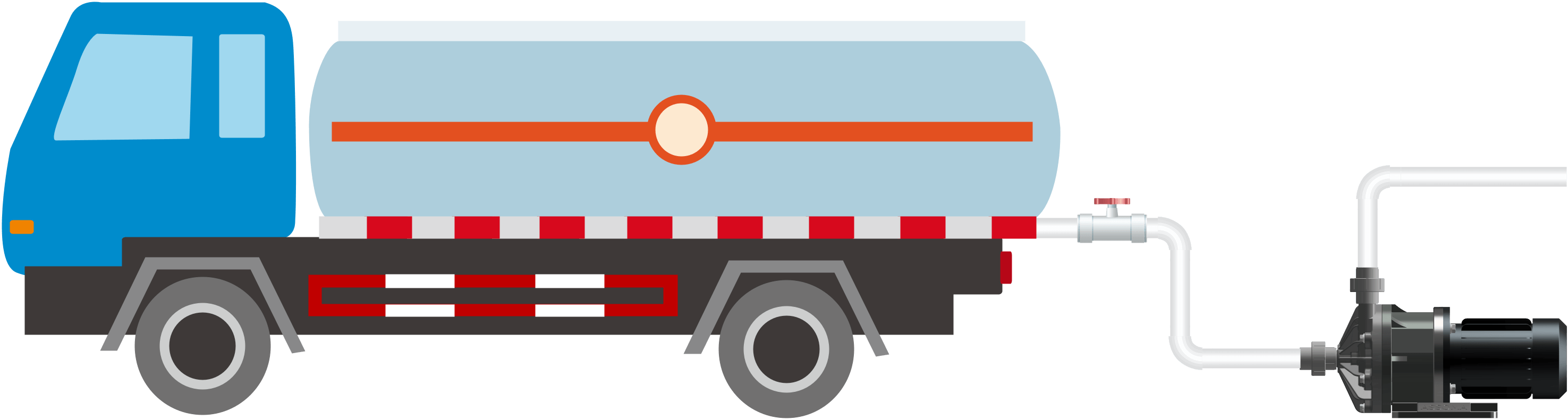
Like the heading described, we are trying to determine the transfer of liquids in a system. Typical
applications include chemical unloading, sump pit drainage, and waste chemical discharge. These applications
have something in common, a fixed container which we are trying to empty, in which we know the storage
capacity of the container.
Chemical unloading: Usually, we want to transfer the chemical as fast as possible, but a higher transfer
rate will require a larger piping diameter and a larger pump. We need to determine the desired unloading
time then calculate the flow rate required to achieve the transfer time.
For example, if we have a small chemical truck with a tank capacity of 3000 liters. We wish to complete the
chemical unloading in under 20 minutes. Therefore, we will need a transfer rate of at least 9000 liters per
hour or 9 m3/h.
Method 2: Circulation rate
Liquid circulation is a very common pump application, especially for production processes. Some
of the applications including electroplating applications, chemical mixing, filtration applications,
etc.
Electroplating application: Suppose you have an electroplating tank with a capacity of 2500 liters. Suppose
you need a circulation rate of 6 cycles per hour to maintain your electroplating quality, then your
circulation rate will be 2500 liters x 6 cycles/hour or 15 m3/h.
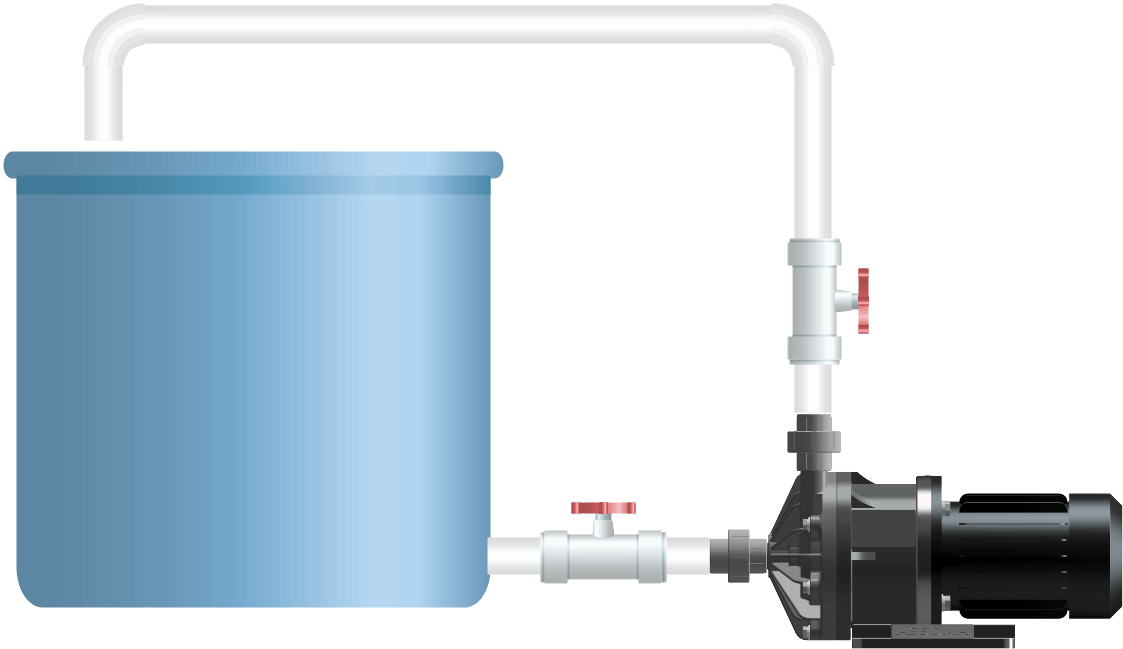
Method 3: Achieving/Maintaining system pressure
Some chemical processes require maintaining a constant discharge pressure such as a nozzle system. In such a system, determine the flow rate through each nozzle. For example, if a nozzle requires a flow rate of 1.5 lpm and the system has 50 nozzles, then the total flow rate will be 75 lpm.
Calculating the total head of a system
The duty point of a pump includes the capacity (flow rate) and the pressure also known as the total head of the system. Some commonly used units of measurement for pressure include psi, kg/m2, bar, etc. The head is expressed as a length, including meters and feet. The total head consists of several components as outlined below.
The total static head
In a pump system, there is the suction system and the discharge system. The pump is used to move the
liquid from the suction tank to the discharge tank. Usually, the discharge tank is higher than the
suction tank, requiring the pump to provide the lift. The amount of vertical distance that the pump
lifts is the total static head.
For the suction system, we would want to consider the lowest liquid level. For the discharge system, we
want to consider the maximum liquid level. Sometimes that means the highest vertical point of the piping
if the piping comes back down before reaching the discharge tank. This way, we can be sure to get the
largest total static head value.
Here are some examples of different scenarios and their total static head.
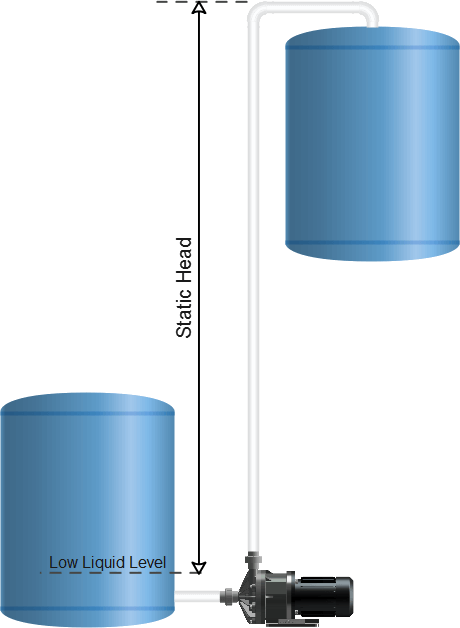
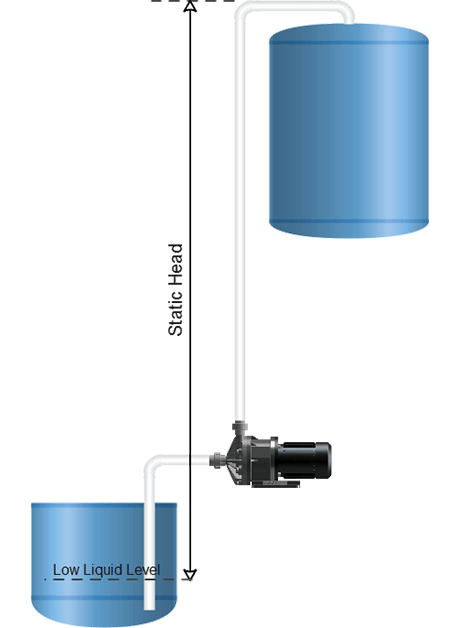
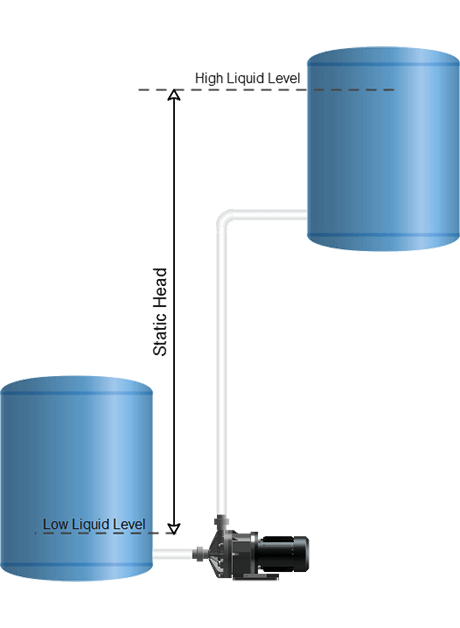
Calculating the velocity head
The velocity head comes into play when the Suction size and the Discharge size are different. The flow
velocity through a larger pipe diameter will be slower than the flow velocity through a smaller pipe
diameter for the same flow rate. Therefore, the changes in flow velocity (energy changes) will result in
energy losses. However, the loss is usually relatively small for most systems, the velocity head is
usually ignored. The systems that we need to pay attention to velocity head are systems with spray
nozzles where the effective diameter is significantly different, and for applications where the liquid
drag is particularly high such as high viscosity liquids or liquids with high fiber content.
Calculating System Resistance (pressure losses)
A large part of the work done by the pump is to overcome the friction against the piping, valves,
fittings, and other equipment such as filters and spray nozzles as the liquid moves through the system.
The frictional losses, also known as system resistance, are observed as pressure drops/losses as the
liquid moves from the suction system to the discharge system. For Newtonian fluids, the losses can be
calculated using various methods to determine the pressure losses. The pressure losses are usually
expressed in meters of equivalent straight piping loss.